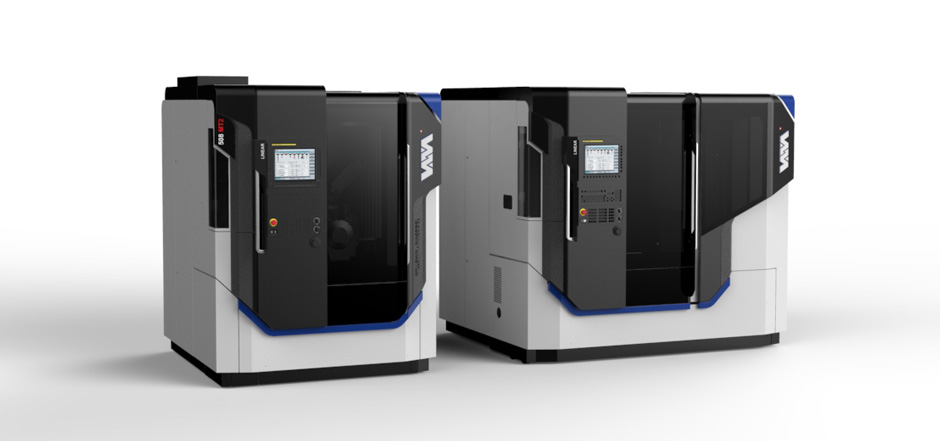
24 Nov Two world premiere high-precision machining centres
The machine manufacturer Willemin-Macodel SA of Delémont presented two global innovations at the EMO Milano. Sharing the same philosophy as their predecessor, the high-precision machining centres 508 MT2 and 508 MT2 X 1000 have benefited from many technological developments and substantial work on ergonomics.
Requirements in terms of flexibility are constantly increasing, especially in the medical field where the production runs are very small and often customised. To meet this need, machines must be developed to enable rapid change from one type of part to another. Minimisation in setting and operation times, research in ergonomics and user-friendliness are now the keywords. Starting from this premise, the Willemin-Macodel engineers have defined the work specifications for their new machining centres focusing on three main points: efficient machine dynamics, high-precision and a thermal stability throughout the manufacturing process.
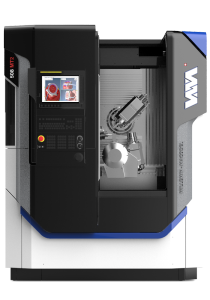
The new machining centre has been redesigned to allow the integration of linear motors on the X-, Y- and Z-axes.
Linear motor drives
Based on an architecture similar to the 508MT, the new machining centre has been redesigned to allow the integration of linear motors on the X-, Y- and Z-axes. Equipped with torque motors on all rotary axes, it guarantees path following and surface finishes of very high quality. Developed inhouse, the key elements of the machine such as the powered spindle, the dividing heads or the turret offer the advantage of perfectly meeting the machine work specifications. Thus, the extremely dynamic powered spindle installed on a B-axis allows change of tool to be done in less than one second (up to 72 tools in the magazine). Apart from these technological advantages, internal development also allows the company to retain mastery over the strategic components of its machines. The stability of the machine, essential to guarantee high part quality throughout the production cycle, is guaranteed above all thanks to a healthy design of the mechanical elements and of the machine providing it with strong basic robustness. To obtain yet better results, Willemin-Macodel has developed a sophisticated algorithm which compensates for the spurious displacements due to the thermal expansion of the items of the force loop and to the kinetostatic effects of the spindles. The machine is thus extremely stable and requires no warm-up cycle to guarantee very high long-term precision, independent of the machining cycles.
Turnkey solutions
To provide its customers with the solutions best adapted to their needs, Willemin-Macodel proposes several additional items of equipment to reply to the work specifications as closely as possible. Thus, an automation system can be added,in a simple version for the unloading of parts for example, or in a more complex variant with a polymorph robot capable of simultaneously performing, in the manufacturing process, operations such as marking, cleaning or installation of delicate parts on pallets. Willemin-Macodel is renowned for the delivery of turnkey machining solutions based on work specifications. The solutions are discussed in partnership with the customers and this is why inhouse control of all these developments is a determining factor. For the configuration of the machine, the user has the choice between several dividing heads for diameters ranging from 37 mm at 8,000 rpm to 65 mm at 3,000 rpm. The user can also choose electric chucks for the A-axis.
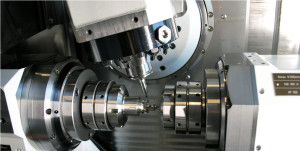
For the configuration of the machine, the user has the choice between several dividing heads for diameters ranging from 37 mm at 8,000 rpm to 65 mm at 3,000 rpm.
Backworking is done by jaws in the simple version but can also be done with a turret proposing 3 effective positions (counter-spindle, jaws and tailstock installed on the U-axis), thus guaranteeing rapid changeovers thanks to the high flexibility of the turret. The 3 effective positions also allow very complex parts with high added value to be manufactured. Some parts can be manufactured only by the multi-position turrent, when these parts require various support and consecutive backworking operations (jaws as support then backworking in tailstock for example).
Design and ergonomics
With a more modern design, or more aggressive in the positive sense of the term, the new Willemin-Macodel machining centres are in step with the markets that they target. High-end markets, with high-added value parts where the notion of “beautiful” is important, as conveying the idea of performance, power and clarity. User comfort has also been re-examined in depth. Access to the core of the machine is facilitated to a great extent, large windowed spaces give an overall view of the work in progress and an innovative system offers several numerical control positions that can accompany the operators in their lateral movements. The control screen has also been resized to 15” to make programming and read of data easier. The various functionalities of the machine are grouped together and are easily accessible for maintenance. The peripherals, which normally are added around the machines, have been integrated. Streamlined in this way, the machine is very compact offering a gain in floor space and facilitating any later movements of the machining centre. The bed, which rests on three points, is made of polymer concrete. This material has highly interesting properties such as high thermal inertia and vibration damping capabilities. Note that this machine is also available in 5-axis version with double dividing head and vertical powered spindle. In this variant, the 508S2 is proposed with the latest generation Fanuc or Heidenhain numerical control. Working in part-by-part mode, this simultaneous 5-axis machining centre is extremely efficient and also allows turning operations to be done at 4,000 rpm on the C-axis dividing head.
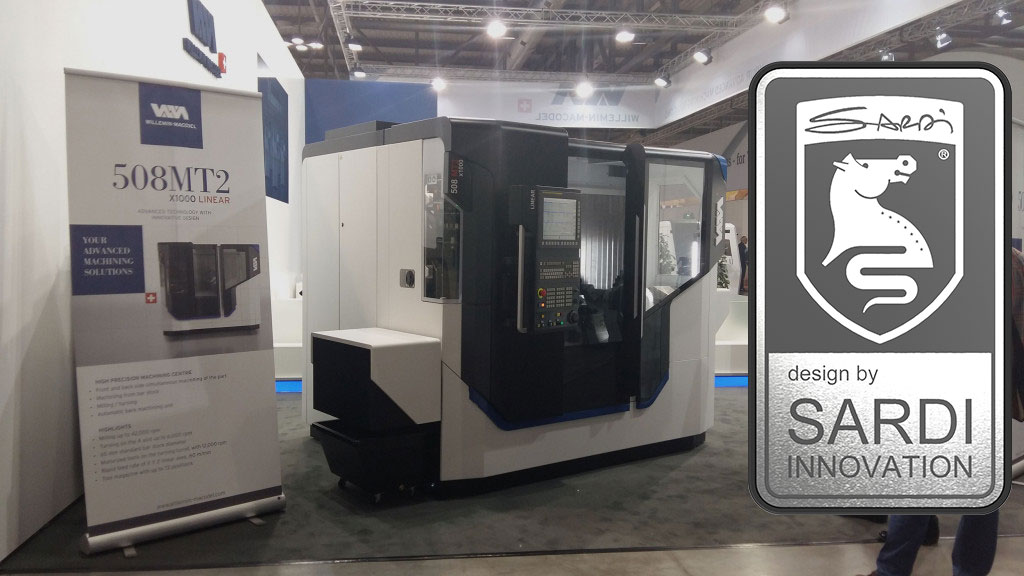
The 508MT2 X1000 machining centre differs from its smaller brother 508MT2 by the travel length X, increased to 1,000 mm.
Simultaneous machining, gains in productivity
The 508MT2 X1000 machining centre differs from its smaller brother 508MT2 by the travel length X, increased to 1,000 mm. The linear motor drive is moreover especially efficient with a travel such as this. This extension allows the installation of a turning turret with 12 driven positions (12,000 rpm). Complementing the backworking turret with 2 effective positions (counter-spindle and jaws), this technical achievement allows simultaneous machining, without compromise, with the powered milling spindle and the turning turret. This configuration also offers high utilisation flexibility and can reduce the down times and therefore the production times by 40 to 45% according to the type of work. To avoid all interference, the programming channels of the two units are of course independent. Although more complex than the 508 MT2, this machining centre allows quick changeovers. Also, on this machine, special care has been taken with the ergonomics and the design. The operator can easily go from a 508MT2 machine to a 508MT2 X1000 machine as many of the components are the same, such as the powered spindle, the rotary axes, the tool magazine or, again, the multi-position backworking turret. No compromises have been made on this machine concerning the accuracy and the quality of the surface finishes. Like the 508MT2 machine, it guarantees strong robustness in your production processes thanks to its perfectly controlled thermal behaviour.
Two world premiere high-precision machining centres.